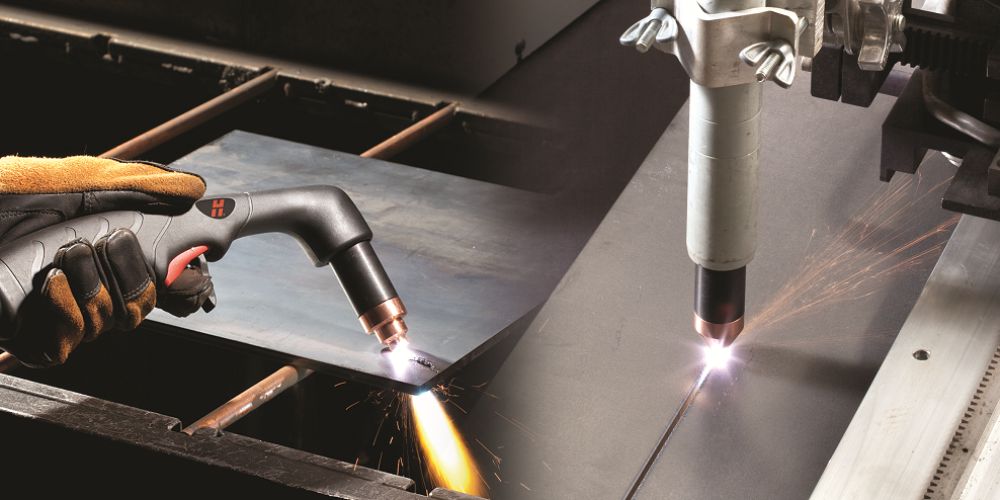
10 LỖI THƯỜNG GẶP KHI CẮT PLASMA
Một người vận hành có kinh nghiệm khi sử dụng Máy cắt plasma được bảo trì tốt có thể tiết kiệm được nhiều giờ lãng phí phải dừng máy và hàng ngàn đô la chi phí hoạt động. Do đó sẽ mang lại lợi nhuận lớn hơn cho quy trình cắt và nhiều lợi nhuận hơn cho công ty.
Với kinh nghiệm gần 20 năm cung cấp sản phẩm cắt Plasma của Hypertherm, Weldtec phân tích 10 lỗi thường gặp và cách tránh mắc phải các lỗi này.
1. Sử dụng phụ kiện cho đến khi hỏng mới thay
Nhìn vào phần phụ kiện hỏng đã thay thế và bạn có thể thấy nhiều phụ kiện đã hỏng nặng. Sử dụng phụ kiện quá hao mòn không chỉ làm giảm chất lượng gia công tấm, mà nó còn là nguyên nhân làm hỏng mỏ và thời gian dừng hoạt động không cần thiết.
Người vận hành có kinh nghiệm có thể phân biệt phụ kiện đã hao mòn chỉ bằng âm thanh phát ra từ mỏ, màu sắc của hồ quang hoặc có sự thay đổi nhỏ của chiều cao của mỏ. Tuy nhiên, cách dễ nhất để biết tình trạng phụ kiện là kiểm tra định kì phụ kiện khi nhận thấy chất lượng cắt đang kém đi.
Ghi chép lại thời gian phải thay thế phụ kiện trung bình (dựa trên số lần đánh thủng hoặc thời gian cắt hồ quang) và tổng hợp thời gian sử dụng phụ kiện dự kiến - dựa trên cường độ dòng điện, vật liệu và độ dày tấm. Khi đã có thời gian sử dụng phụ kiện trung bình, người vận hành sẽ biết khi nào nên kiểm tra hoặc thay thế phụ kiện mới để giảm các nguy cơ có thể xảy ra.
2.Thay đổi phụ kiện quá sớm
Trái ngược hoàn toàn với điều 1 là việc thay thế phụ kiện quá sớm (tuy nhiên ít khách gặp phải trường hợp này). Thay vì thay phụ kiện sau một số giờ sử dụng tiêu chuẩn, người vận hàng nên kiểm tra lại mức độ hao mòn của phụ kiện.
Liệu bép cắt có bị vết cắt ở trong hay ngoài? Liệu vòng đệm có còn tròn không? Nếu có, nghĩa là cần thay phụ kiện mới. Nếu không vẫn có thể dùng được. Để kiểm tra điện cực, cần xem phần hafnium ở ngay giữa của điện cực và cần thay thế nếu không còn.
Vòng xoáy khí chỉ nên thay nếu kiểm tra thấy có vết bẩn, có mỡ trong các lỗ, có vết nứt, vết cháy hồ quang, hoặc bị mòn vẹt nhiều. Cũng tương tự như vậy với chụp bảo vệ, chỉ nên thay thế khi có hư hỏng. Thông thường chụp bảo vệ chỉ cần làm sạch khỏi xỉ kim loại là có thể sử dụng tiếp.
3.Cài đặt sai thông số và sử dụng sai phụ kiện
Lựa chọn phụ kiện dựa theo vật liệu và độ dày cắt, cường độ dòng điện và loại khí sử dụng cắt plasma và các thông số cắt khác. Sổ tay vận hành đi kèm với hệ thống plasma sẽ cho bạn biết loại phụ kiện nào là phù hợp.
Sử dụng không đúng phụ kiện có thể dẫn tới giảm tuổi thọ và chất lượng cắt. Ngoài ra lưu ý cần phải vân hành đúng của cường độ dòng điện của loại phụ kiện. Để đạt chất lượng cắt tốt nhất và tăng tuổi thọ phụ kiện khi cường độ dòng điện đạt 95% của chỉ số bép cắt. Nếu cường độ dòng điện yếu, mạch cắt sẽ rất xấu. Nếu quá cao, tuổi thọ của bép cắt sẽ bị ảnh hưởng.

Các phụ kiện trong mỏ cắt cần được căn chỉnh chính xác và lắp khít với nhau nhằm đảm bảo tiếp xúc điện tốt và dòng khí chạy chính xác và chất làm mát thông qua mỏ. Khi thay đổi phụ kiện, nên giữ các vật liệu tiêu hao tại nơi sạch sẽ để tránh bụi bẩn hoặc bụi kim loại làm bẩn mỏ.
Đảm bảo khi lắp mỏ phải sạch là việc rất quan trọng và thường bị bỏ qua. Khi bôi trơn vòng O-ring, sử dụng vừa đủ chất bôi trơn để làm bóng O-ring. Quá nhiều chất bôi trơn có thể gây tắc nghẽn và làm bẩn mỏ, dẫn đến hồ quang không kiểm soát khi sản sinh plasma và dẫn đến hỏng mỏ. Không bao giờ sử dụng mỡ. Nếu có thể gây nứt và cháy mỏ.
5.Không bảo trì thường xuyênTuổi thọ của mỏ có thể kéo dài hàng tháng hoặc thậm chí hàng năm nếu được chăm sóc hợp lý. Giữ ren của mỏ sạch và kiểm tra rãnh tìm các chất bẩn và hư hại. Làm sạch bụi bẩn, bụi kim loại hoặc chất bôi trơn dư thừa bằng cách sử dụng miếng gạc bông và chất làm sạch tiếp xúc điện hoặc chất tẩy Peroxyt.
6.Không kiểm tra lưu lượng khí và lưu lượng dung dịch làm mátKiểm tra lưu lượng khí, áp suất và mức dung dịch làm mát mỗi ngày. Nếu lưu lượng không đủ, phụ kiện sẽ không được mát và làm giảm tuổi thọ. Không đủ dung dịch làm mát do mòn máy bơm, bộ lọc bị tắc, mức dung dịch làm mát thấp v.v… là nguyên nhân phổ biến gây ra sự cố hệ thống.
Áp lực khí đều rất quan trọng để duy trì hồ quang cắt. Áp suất khí quá cao là nguyên nhân phổ biến của "lỗi khởi động", khi mà mỏ không thể khởi tạo hồ quang khi tất cả các điều kiện khác đều ở mức hoạt động bình thường.
Quá nhiều áp lực khí cũng sẽ làm điện cực nhanh bị hỏng. Tương tự như vậy, nguồn cấp khí plasma phải được giữ sạch để tránh làm giảm tuổi thọ của phụ kiện và mỏ. Các hệ thống khí nén đặc biệt dễ bị dầu, hơi ẩm và nhiễm bẩn.
7.Đánh thủng quá thấp
Điểm dừng đánh thủng, khoảng cách giữa phôi và đầu mỏ, là yếu tố quan trọng cho cả chất lượng cắt và tuổi thọ của các chi tiết. Ngay cả những thay đổi nhỏ về chiều cao mỏ cũng có thể ảnh hưởng đến góc của mặt cắt.
Chiều cao của mỏ trong quá trình đánh thủng là đặc biệt quan trọng. Một lỗi thông thường mà người vận hành hay mắc phải là đánh thủng quá thấp. Điều này làm cho kim loại nóng chảy bắn tóe ra phía trước bép cắt và chụp bảo vệ.
Hồ quang thậm chí có thể “tắt” ra khi mỏ đánh thủng tại điểm chạm kim loại, hoặc kéo dọc theo bề mặt trong khi cắt. Nếu hồ quang "tắt”, các bộ phận tiêu hao và đôi khi kể cả mỏ cũng bị phá hủy. Cần đánh thủng ở chiều cao 1,5 đến 2 lần chiều cao cắt khuyến cáo.
8.Cắt quá nhanh hoặc quá chậmCắt quá nhanh hoặc quá chậm sẽ gây ra vấn đề về chất lượng cắt. Nếu tốc độ quá chậm, các mảnh cắt sẽ có "xỉ do cắt chậm", là lượng xỉ bọc tích tụ dọc theo cạnh dưới mạch cắt. Tốc độ cắt chậm cũng có thể làm mạch cắt lớn hơn và bắn tóe trên tấm kim loại nhiều.
Nếu tốc độ cắt quá nhanh, hồ quang sẽ lùi lại trong mạch cắt gây cạnh vát, độ bù mạch cắt hẹp, và một hạt xỉ nhỏ cứng cứng dọc theo cạnh dưới cùng của mạch cắt. Xỉ do tốc độ cắt cao rất khó loại bỏ. Tốc độ cắt chính xác sẽ tạo ra ít xỉ nhất, mạch cắt sạch, làm giảm việc xử lý lại trước khi đưa vào gia công.
9.Kéo giãn hồ quangViệc kéo giãn hồ quang có thể xảy ra khi bắt đầu cắt và khi cắt xong. Hồ quang cắt vào thành bép cắt – gây hỏng bép cắt. Khi cắt từ ngoài vào, hồ quang plasma nên được bắt đầu với lỗ bép cắt trực tiếp đặt giữa cạnh của mảnh cắt. Điều này rất quan trọng khi đột dập/ đục lỗ / cắt plasma khi hồ quang được khởi tạo ở trung tâm của một lỗ đột.
Với ứng dụng này, hồ quang có thể được khởi tạo từ cạnh và không phải là trung tâm của lỗ. Sự kéo giãn của hồ quang cũng có thể xảy ra ở cuối đoạn cắt nếu mỏ được lập trình để chạy khỏi tấm khi vẫn còn hồ quang, hoặc nếu đường “dẫn ra” đi theo mạch cắt của kim loại đã cắt trước đó. Tính được thời điểm tín hiệu “tắt hồ quang” và lập trình đường “dẫn ra” có thể giảm thiểu hiệu ứng này

Tấm cong vênh và va chạm có thể làm mỏ hỏng mà không thể sửa chữa được. Có thể phòng tránh va chạm với phần phôi bằng cách lập trình hệ thống cắt hình để di chuyển xung quanh, chứ không phải phía trên, phần cắt.
Cảm biến chiều cao của mỏ cũng phòng tránh va chạm mỏ bằng cách điều chỉnh các biến số trong vật liệu. Tuy nhiên, điện áp tạo ra nhờ cảm biến chiều cao có thể không bảo vệ được mỏ. Ví dụ, "mỏ chúi thấp" thường xảy ra ở cuối của chu trình cắt khi mỏ đi theo mạch cắt quá lâu. Điều này được thực hiện để bù đắp cho điện áp tăng dần lên khi hồ quang giãn ra.
Lập trình cẩn thận của chức năng điều khiển chiều cao mỏ và hướng dẫn ra có thể giảm thiểu được điều này. Cuối cùng, thiết bị ngắt gắn mỏ có thể giúp ngăn ngừa mỏ bị hỏng nếu có va chạm.
Những lỗi thường gặp như trên tưởng chừng rất bình thường nhưng ảnh hưởng rất nhiều đến năng suất, phí tổn mà Quý khách có thể mắc phải. Weldtec xin giới thiệu đến Quý khách các sản phẩm chính hãng máy cắt Plasma của Hypertherm phù hợp với từng vật liệu mà Quý khách đang sử dụng.